Vacuum blasting
For preparing and cleaning steel surfaces, different types of abrasive blasting are possible. For example, we know the common techniques of sandblasting, wheel blasting, bead blasting, vapor blasting and blasting with alternative abrasives such as glass or plastic, but also vacuum blasting is part of the abrasive blasting possibilities. These techniques are often used to remove rust, mill scale, copper slag, coatings and other dirt. But what is vacuum blasting anyway? How does it work, and what are the differences with the other abrasive blasting techniques?
Vacuum blasting: what is it?
Vacuum blasting is in many ways similar to the other forms of abrasive blasting. In general, vacuum blasting works the same. When a surface is prepared by vacuum blasting, a combination of air and an abrasive is applied to the surface at high pressure. So far there are no differences with the other blasting techniques. Yet there is one major difference between vacuum blasting and the other forms of blasting. This is in the handling of the dust and dirt released during blasting. While sandblasting or glass or plastic blasting, for example, release dirt and dust into the air, vacuum blasting collects it immediately inside the blasting machine. Therefore, the blasting machine in this form of abrasive blasting serves as a dustless sandblaster with a vacuum system.
The benefits of vacuum blasting
When cleaning and preparing steel surfaces, a large amount of dirt can normally be generated during the blasting process. This dirt is often a combination of the abrasive that is used in combination with the dirt that disappears from the surface which is cleaned. A major advantage of vacuum blasting is that this dirt is immediately collected with this technique. This saves a lot of mess and clean up after the blasting process. The material that is collected is sorted and can then be reused as blasting media. Moreover, the dirt and dust that is released in other abrasive blasting techniques can be very harmful to the environment, which is not the case with vacuum blasting.
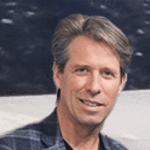
Frits Doddema
Author of MontiPower®
Leadership | Sales | Marketing | Development
He is passionate about alternating solutions which make a true difference. Nothing is impossible is his credo. To make the impossible possible, Frits and the management believe in just one idea to make it happen and to turn the company in a great firm. The innovative approach for game-changing blasting and paint solutions is hands-on keeping in mind the difficult field circumstances for operators, respecting nature and long term costs. The mission is to avoid any disagreement over quality of prep work and coating. Frits and his team push for non-hazardous long term corrosion prevention solutions to overcome any hassle out of a coating job ensuring the best possible bond. The world’s best coatings deserve the world’s best surface preparation. Like in daily life, preparation is everything. From different perspectives like Safety, Health, Ergonomics, Productivity, Recyclability, Co2 neutrality of the plant and the coating process, Substrate Compatibility, Corrosion Resistance, Frits and team are driven to come with improved unique contribution solutions to existing and new end markets.
News
The latest news about us