The alternative to blasting with copper slag
Copper slag is a material that is used in various industries for different purposes. But what exactly is copper slag, and how is it created? To answer this question, we take a look at the melting and refining process of copper. Copper slag is in fact a material that is created during the melting of copper. During this melting, a large amount of soot and rock are created. The combination of these materials is called copper slag. Although copper slag was initially created as a by-product, today it is used in many ways. Among other things, it serves as a filling material in construction and an alternative to sand in the production of concrete. But that’s not all; copper slag is primarily used as an abrasive in the cleaning and preparing of various surfaces.
What is copper slag blasting?
The use of blasting media is a widely used technique for preparing, cleaning and machining steel and other metal surfaces, for example. Copper slag is one of the possible abrasives that can be used. Other blasting media that can be considered are sand, glass, plastic or water. Blasting with copper slag is generally done for two different purposes. First of all, copper slag blasting is an effective way to remove mill scale, rust, dirt, paint and other coatings from metal surfaces. But copper slag blasting also serves another purpose. In fact, blasting can also be used to create a surface profile in a surface. By using copper slag blasting to produce a profile in the surface, it creates an adhesion layer for any new coating.
How does copper slag blasting work?
As mentioned, there are several different techniques available when it comes to blasting, of which the use of copper slag as a blasting agent is one. In general, blasting with copper slag works in the same way as all other blasting techniques. Blasting with copper slag consists of two ingredients. For cleaning and preparing of metal surfaces, the copper slag is combined with air. This combination of air and copper slag is then applied with a very high force to the surface. Because of the great force with which the copper slag is released onto the surface, dirt, rust, mill scale, paint and coatings are easily removed from the object. In addition, due to the violent impact of the copper slag into the metal surface, not only are dirt and coatings removed, but also the surface profile is created which serves as a new adhesion layer.
What are the disadvantages and dangers of copper slag blasting?
Blasting with copper slag has been performed successfully for many years. However, over the years, more and more disadvantages and dangers of blasting with copper slag have come to light. First of all, blasting with copper slag is not without danger. Studies have shown various dangers of working with copper slag. For example, various types of slag, including copper slag, can disintegrate into small particles during blasting. Inhaling these particles can result in unpleasant lung complaints. In some cases, copper slag can also contain traces of toxic metals such as arsenic, beryllium and cadmium. These metals not only have a negative effect on human health, but can also contribute to the pollution of air and water.
The health risks are not the only drawbacks to blasting with copper slag. While blasting can be very effective for removing dirt and coatings, this cleaning technique is not applicable to all materials. Some materials will be vulnerable to copper slag cleaning, which, if not done carefully, will cause damage to the surface. Partly because of this, it is not easy to blast with copper slag yourself, and it is recommended that you always have a professional do it for you. It makes blasting with copper slag not only a dangerous cleaning technique, but also a relatively expensive and time-consuming one.
The alternative to copper slag blasting: MontiPower
MontiPower’s Bristle Blaster® and MBX® are the latest techniques in the field of cleaning and preparing metal surfaces. With their simple and effective operation, the tools are the alternative to blasting with copper slag. The power tools of MontiPower provide the same result as the various blasting techniques, but without the previously mentioned disadvantages. First, the Bristle Blaster® and MBX® by MontiPower are very easy to use. As a result, you can use the tools yourself and you are no longer dependent on professional parties for the cleaning and preparing of your metal surfaces. But that is not all. Because no abrasive such as copper slag is used, the Bristle Blaster® and MBX® are also completely safe to work with and you don’t have to worry about any health issues known from blasting with copper slag. It makes MontiPower’s power tools the perfect alternative to sandblasting, blasting with copper slag and other blasting methods.
How does the alternative copper slag blasting process work?
MontiPower’s Bristle Blaster® and MBX® are hand-held tools characterized by their rotating brush. The Bristle Blasters feature specially designed patented brush tips that stand out for their curved ends. The rapid rotation of the brush quickly and effectively rids metal surfaces of paint, dirt, rust and coatings. The distinctive curvature of the brush tips are of great importance in this regard. During rotation, these points are stopped for a very short time by the so-called ‘accelerator bar’. Due to the small hiccup that occurs here in the rotation process, the curved brush tips are launched with extra great force from behind this bar. Due to the high impact with which the brush comes into contact with the surface, dirt, paint, rust and coatings are not only effectively and precisely removed, but a surface profile is also created that can be used as a new adhesive layer for a new coating.
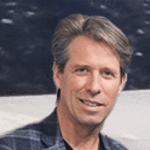
Frits Doddema
Author of MontiPower®
Leadership | Sales | Marketing | Development
He is passionate about alternating solutions which make a true difference. Nothing is impossible is his credo. To make the impossible possible, Frits and the management believe in just one idea to make it happen and to turn the company in a great firm. The innovative approach for game-changing blasting and paint solutions is hands-on keeping in mind the difficult field circumstances for operators, respecting nature and long term costs. The mission is to avoid any disagreement over quality of prep work and coating. Frits and his team push for non-hazardous long term corrosion prevention solutions to overcome any hassle out of a coating job ensuring the best possible bond. The world’s best coatings deserve the world’s best surface preparation. Like in daily life, preparation is everything. From different perspectives like Safety, Health, Ergonomics, Productivity, Recyclability, Co2 neutrality of the plant and the coating process, Substrate Compatibility, Corrosion Resistance, Frits and team are driven to come with improved unique contribution solutions to existing and new end markets.
News
The latest news about us