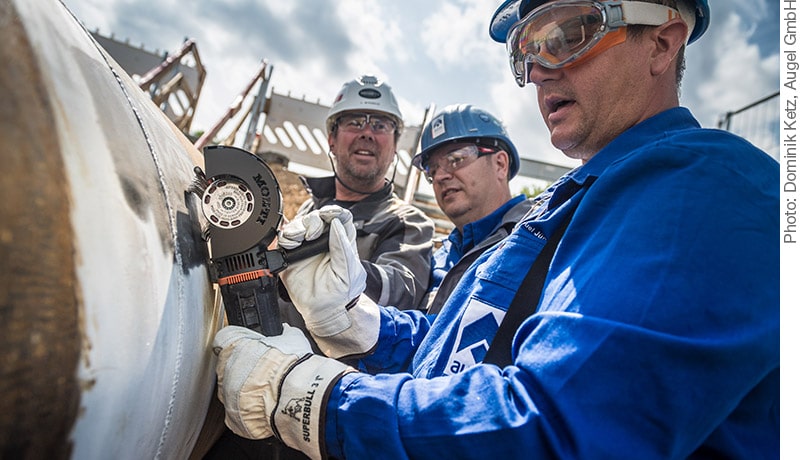
Alternative to bead blasting
Alternative to bead blasting
If you’re looking for a more environmentally-friendly and efficient alternative to bead blasting, Bristle Blasting may be the solution you’ve been searching for. The Bristle Blaster® and MBX® from MontiPower are hand-operated tools, which are equipped with a rotating brush. These specially designed brushes are characterized by their sharpened flexible tips with kneed ends. Not only is Bristle Blasting gentle enough to use on delicate surfaces like chrome and glass, but it also leaves behind a smoother finish compared to traditional bead blasting methods.
What is bead blasting
Bead blasting is a type of surface finishing process that uses small glass beads to clean, smooth, or remove surface deposits from a material. The beads are blasted onto the surface at high pressure to achieve the desired results. This process is commonly used in industries such as automotive, aerospace, and manufacturing to prepare surfaces for painting or coating.
Why use an alternative to bead blasting?
One compelling reason to consider using an alternative to bead blasting is the potential for damage to delicate surfaces. While bead blasting is effective for removing rust, paint, and other surface imperfections, it can also be too abrasive for certain materials. Using a gentler alternative such as Bristle Blasting or vapor can help prevent unwanted scratching or pitting on sensitive surfaces. This alternative method allows for more precise control and can achieve excellent results without risking damage.
The alternative to bead blasting Bristle Blaster® and MBX®
With the power tools from MontiPower, sandblasting is a thing of the past. No sand and no blasting tools; With the Bristle Blaster® and MBX® you can quickly and easily clean surfaces from corrosion and other layers of dirt. Not just cleaning; the patented technology of the power tools also ensures that the surface can be easily processed. It makes Bristle Blaster® and MBX® the only power tool in the world that can ‘sandblast’ with a comparable quality of the original blasting method.
How do the alternative bead blasting tools work?
The Bristle Blaster® and MBX® are hand-operated tools, equipped with a rotating brush. Due to the special designed curved appearance of the tips of the brush, the surface is cleaned quickly and easily with a comparable kinetic energy to traditional sandblasting. Because the tips are released with great force from behind the accelerator bar of the tools, the tips immediately retract from the surface, providing the same micro-structure in the surface as sandblasting. In this way, the Bristle Blaster® and MBX® offer all the benefits of sandblasting, including the high-quality result. This makes MontiPower’s power tools the perfect alternative to sandblasting. An alternative that can be used for many purposes.
Passive corrosion protection is essential to pipeline safety. During construction and repairs, the pipe surface needs to be prepared before the passive corrosion protection system can be applied to ensure long-term protection. This is usually done by sandblasting the surfaces. 3R magazine talked to André Prytamannyi, project director at Augel GmbH, and Uwe Boensch, National Sales Manager at MONTI – Werkzeuge GmbH about experiences with using this technology and its technical details.
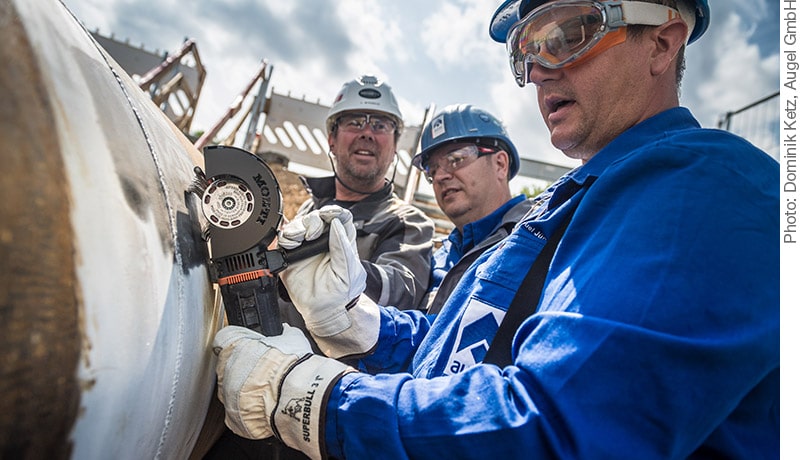
3R: Mr. Boensch, MONTI – Werkzeuge GmbH is celebrating its 30th anniversary this year. How did everything start and what led to developing the Bristle Blaster?
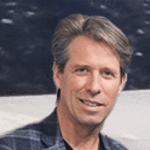
Frits Doddema
Author of MontiPower®
Leadership | Sales | Marketing | Development
He is passionate about alternating solutions which make a true difference. Nothing is impossible is his credo. To make the impossible possible, Frits and the management believe in just one idea to make it happen and to turn the company in a great firm. The innovative approach for game-changing blasting and paint solutions is hands-on keeping in mind the difficult field circumstances for operators, respecting nature and long term costs. The mission is to avoid any disagreement over quality of prep work and coating. Frits and his team push for non-hazardous long term corrosion prevention solutions to overcome any hassle out of a coating job ensuring the best possible bond. The world’s best coatings deserve the world’s best surface preparation. Like in daily life, preparation is everything. From different perspectives like Safety, Health, Ergonomics, Productivity, Recyclability, Co2 neutrality of the plant and the coating process, Substrate Compatibility, Corrosion Resistance, Frits and team are driven to come with improved unique contribution solutions to existing and new end markets.
News
The latest news about us