10 types of abrasive blasting
There are several types of blasting methods, in this article we will tell more about the differences and different types of blasting methods.
Bristle blasting
The Bristle Blaster® and MBX® from MontiPower are the new developments in the field of surface preparation. Due to the specially developed technology with patented brushes, the power tools are the perfect alternatives for the existing blasting equipment.
With the use of the Bristle Blaster® and MBX® from MontiPower, blasting with different types of loose abrasives is a thing of the past for smaller areas and difficult to access areas. The tools are easy to use, are – unlike blasting – completely safe and very effective. Not only in cleaning surfaces, but also in processing them.
With their impact, the brushes of the power tools create a profile on the surface that can be compared to the surface profile that is created after blasting. In this way, MontiPower tools are the ideal alternative to sandblasting.
Bead blasting
Bead blasting has become an increasingly popular method of surface treatment. It is an effective and efficient method for removing dirt and oxidation from different materials.
There are various surface preparation techniques available to use and choose from. Abrasive blasting is the most well-know form of surface preparation. This method is often used for removing coatings, mill scale, paint and other dirt. In most cases, abrasive blasting involves applying air and an abrasive media with great force to the surface. This results in the removal of the material from the object. There are many different types of media to blast with. A few examples of blasting techniques with different media are: sandblasting, vapor blasting, vacuum blasting, wheel blasting and bead blasting. All these options have their own advantages and disadvantages. It this article, we will focus on bead blasting.
Centrifugal blasting
Centrifugal blasting is a type of surface finishing process where a metal surface is blasted by an abrasive material that is propelled by a centrifugal force. The process sprays the abrasive material onto the surface at a high velocity. This process is commonly used to remove scale, corrosion and burrs from a metal surface. In addition, it can be used to clean, roughen or texturize a surface or as a form of shot peening. Centrifugal blasting also provides a unique way to etch and debur surfaces. Many surface preparation projects may require manual cleaning if centrifugal blasting is not used.
Dry ice blasting
Dry ice blasting, or CO2 blasting is a technique of cleaning where solid CO2 is accelerated in a pressurized air flow and focused on a surface to clean it.
This technique is a very clean alternative compared to other blast cleaning methods. It can be used to clean surfaces. It is used to get rid of dirt, oil, paint, or strip pollutants from a surface. Dry ice blasting doesn’t cause contaminants to build up in the waste and dramatically lowers the secondary waste that needs to be thrown away.
Pencil blasting
Pencil blasting is a process of using a technique similar to “burning in” with a pencil-shaped brush. This type of blasting is often used as a way to get into areas of difficult access where heavier sandblasting is not recommended or possible. By choosing the correct material, size and shape of the media used in the process, it is possible to achieve clean, smooth finishes with minimal to no warping or crack damage. It is a common choice for the repair or blasting of raw metals, masonry, wood, plastic and other materials, as it is a more gentle and precise process than heavier blasting methods.
Sandblasting
Sandblasting involves blasting a combination of sand and air under high pressure onto the surface that has to be prepared or cleaned. Due to the high force with which the sand is applied to the surface, mill scale, dirt or any coatings are easily removed. Moreover, the sand creates a structure in the surface, which makes it easy to apply a new layer. However, despite its advantages, sandblasting also has a large number of disadvantages. For example, sandblasting is very dangerous to our health. But why is sandblasting actually so dangerous? And what are the risks?
Soda blasting
Soda blasting is a mild form of abrasive blasting using sodium bicarbonate particles and compressed air, which has a gentler effect than sandblasting.
Soda blasting involves the use of compressed air to blast particles of sodium bicarbonate with a much lower intensity than traditional abrasive blasting techniques, such as sandblasting. Soda blasting is a more gentle form of abrasive blasting. It is used to clean, strip and finish surfaces in which it causes less damage and doesn’t create hazardous substances or dust.
Steel grit blasting
Steel grit blasting is a process where metal is blasted with a small amount of compressed air and steel particles. This process can be used to clean, strip, and prepare surfaces before a fresh coat of paint or finish can be applied. The steel grit blasting process is a popular choice for many projects since it is both less abrasive and cost effective. Additionally, steel grit blasting is versatile and can be used on many different surfaces. This process is often used on metals, plastics, and wood. The steel grit blasting process is a quick and effective way to change the look of a surface by removing rust, old paint and any other contaminants that may have collected on the surface over time.
Vacuum blasting
Vacuum blasting is an abrasive blasting process that uses a vacuum to capture material during the blasting process. This process is gaining popularity in many industries due to its ability to reduce air pollution, dust, and other airborne hazards. Vacuum blasting is a dry process meaning that little or no media, cleaning agents, or water are used in the blasting process. Vacuum blasting works by using large amounts of vacuum pressure to capture the blasting media as the blasting takes place. The vacuum then filters, cleans and collects the blasting media, making it possible to reuse the same media for multiple jobs. Vacuum blasting is an effective and environmentally-friendly option for surface cleaning, paint and rust removal, and most other abrasive blasting applications.
Wet blasting
Wet blasting is a process used for the surface preparation of metals, plastics, or other materials. During this process, a high-pressure abrasive slurry is delivered to the surface. This slurry is composed of a mix of an abrasive (such as aluminum oxide or silicon carbide), water, and a detergent (which helps keep the slurry suspended and separates the abrasive debris from the surface being treated). The combination of the high-pressure stream and the suspended abrasive in the slurry blasts the surface, providing a superior surface finish that can be used for various finishes or preparation for powder coating or other processes. Wet blasting is a much more efficient process than dry blasting and produces less dust and debris, making it ideal for use in sensitive environments such as aerospace or electronics.
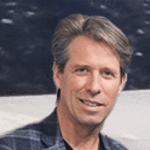
Frits Doddema
Author of MontiPower®
Leadership | Sales | Marketing | Development
He is passionate about alternating solutions which make a true difference. Nothing is impossible is his credo. To make the impossible possible, Frits and the management believe in just one idea to make it happen and to turn the company in a great firm. The innovative approach for game-changing blasting and paint solutions is hands-on keeping in mind the difficult field circumstances for operators, respecting nature and long term costs. The mission is to avoid any disagreement over quality of prep work and coating. Frits and his team push for non-hazardous long term corrosion prevention solutions to overcome any hassle out of a coating job ensuring the best possible bond. The world’s best coatings deserve the world’s best surface preparation. Like in daily life, preparation is everything. From different perspectives like Safety, Health, Ergonomics, Productivity, Recyclability, Co2 neutrality of the plant and the coating process, Substrate Compatibility, Corrosion Resistance, Frits and team are driven to come with improved unique contribution solutions to existing and new end markets.
News
The latest news about us